産業用ネットワークソリューション / 製造業
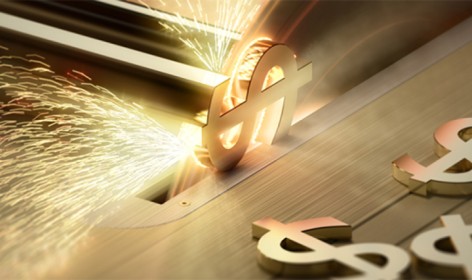
IIoTがマニュファクチャリングのデータを利益に変える2つの方法
製造業のデジタル化と運用をIIoTに接続することには明らかに利点がありますが、製造業界はいくつかの理由でこれに躊躇しています。それらの主な理由は、緊急性と技術担当者の不足、新しい機器の導入に伴う追加の投資と稼働停止コストからです。さらに、工場作業員がデジタル化に抵抗し、スムーズに稼働している工場に混乱を引き起こす可能性があるという懸念が、変革に関するすべての議論を停止させることもあります。 これは、先に進むよりも通常どおり続行する方が安全であるように思われることが理由だと考えられます。しかし、パンデミックをきっかけに、企業は現状のままでは継続できないことに気づいています。生産を継続し、競争力を維持するためには、無人運用が急速に必要となっています。無人運用はデジタル化の明らかなメリットですが、それだけではありません。
デジタル化は、現在の障害に対処するだけでなく、製造実行システム (MES) と組み合わせて生産効率を向上させる豊富なリアルタイムデータを提供します。たとえば、稼働率 (UT) が低いと、生産サイクルが長くなり、注文充足率が低下し、残業コストが高くなります。これまでは情報が不十分であったため、製造会社は問題を特定するのに苦労し、解決するのも困難でした。IIoTを通じて、機器からデータを抽出して分析することで、運用上のボトルネックを発見できます。これらの洞察は、管理者に視覚的に提示され、生産を最適化するのに役立ちます。
正しいデータ = 正しい洞察:十分な情報を得る力を認める
Moxaは顧客との取り組みの中で、これらの例を見てきました。あるとき、IIoTを導入して機器からの電流信号データを収集し、機器の稼働時間を測定しているエンジン部品メーカーに協力しました。当初、メーカーはUTの低下という重大な問題に直面しており、徹底的な調査が必要でした。調査の結果、同社のMESは、従業員の勤怠を記録する手動のタイムカードシステムと連動していることがわかりました。手動システムでは、夜間勤務の従業員が作業を行なわなくても超過勤務手当がつくようになっていました。しかし、MESが従業員の出退勤時間を機械の稼働時間と認識していたため、データに不整合が生じており、より長い稼働時間が誤って表示されていました。IIoTにより、運用管理者は、毎日提供される機器自体からの正確なデータを通じて、累積生産量をよりよく理解することができるようになりました。夜勤のUTは改善され、上級管理者は週次と月次の改善を定期的に追跡できるようになりました。1年半にわたるテストの結果、機器の稼働率は70%から82~85%に増加しました。これにより生産サイクルが改善し、従業員の残業時間も大幅に削減されました。
1%のイールド (利回り) = 1%の利益率:AIが今日のデータを明日の利益に変える
ファクトリーで幅広く使用されているIIoTアプリケーションは、収集したデータの利用方法に応じて、さまざまな運用上の問題を解決することができます。そのひとつが、収集したデータにAIを活用して予知保全を可能にするアプリケーションです。IIoTに接続されたマシンにセンサーを追加すると、データをリアルタイムでクラウドに送信できます。その後、バックエンドのAIプラットフォームは、振動、温度、回転速度、電流などに関する収集されたデータを分析して、制御基準を確立し、変動をチェックできます。これにより、モニタリングの結果が大きく異なるような事態が発生する前に、予知保全を行うことができます。また、マシンの切削工具の電流周波数の測定値が高すぎる場合、工具の損傷を分析できます。この分析により、破損の可能性がある工具を早期交換できるようになり、予期しないダウンタイムや事故が減少します。その結果、生産のイールドが向上し、機器のメンテナンスコストを削減できます。その他の一般的なアプリケーションには、資材管理、生産計画、スケジュールの最適化などがあります。IIoTを使用してデータを分析し、予測することによって、企業は予防的に行動し、単純なデータを効果的に実際の利益に変えることができます。
これまでの世界各地の事例を見ると、多くの企業がIIoTを使用して生産効率を向上させてきました。 無人化が進むファクトリーにおけるIIoTアプリケーションの利用範囲はますます広がり、多様化しています。
予知保全の詳細については、下記の技術情報をご覧ください。