産業用ネットワークソリューション / OTセキュリティ / 製造業
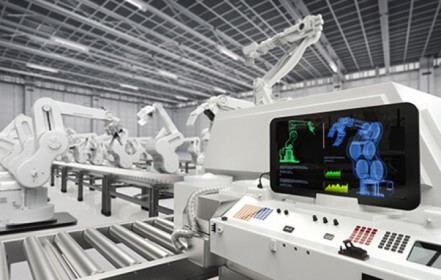
Industry 4.0の時代に対応
Industry 4.0の時代に対応するスマートなマニファクチュアリングを実現
過去数年間にわたる技術の進歩は、製造業界に多大な影響を与え、スマートファクトリとして一般に知られている現象を引き起こしています。スマートファクトリの核心は、データ収集であり、生産および組立ラインにおける多くのセンサ、モータ、およびロボットに大きく依存しています。
スマートファクトリが製造業の未来としてうたわれているのには正当な理由があります。製造業者は、厳しくなるグローバル競争、より短い製品サイクル、および変化する顧客の要望に対処しなければならず、これらすべてが生産スケジュール、効率性、および利益率に圧力がかかっています。柔軟性、効率、およびスループットを向上させるには、データ収集を可能にするディジタルコネクティビティがこれらの目標を達成するための鍵となります。この記事では、製造現場でのスマートマニュファクチャリングの利点を説明するために、マスカスタマイゼーション、予知メンテナンス、およびリモート監視の3つのアスペクトに焦点を当てます。
マス顧客イゼーションの実装
今日の消費者は、カスタマイズされたオン要望で入手可能な製品をますます望む傾向にあるため、製造業における大量カスタマイゼーションへの移行が推進しています。更に、マスカスタマイゼーションは、大量生産品の価格で個別のカスタマイズされた製品を顧客に約束します。マスカスタマイゼーションを実現するために、顧客のカスタムオーダは、Enterprise Resource Planning(ERP)システムまたは他のスマートアプリケーションにインテリジェントに統合され、必要に応じて上流の材料をオーダできるように在庫システムとマッピングされます。これらのシステムとアプリケーションは、その後、Advanced Planning&Scheduling System(APS)およびMES/SCADAシステムに接続して標準化、大量生産、カスタム生産、および混合モデルの生産を開始します。
マスカスタマイゼーションは、標準化された製品とカスタマイズされた製品の両方をサポートするために、いくつかの異種のスマートマシンで構成されるスマート生産ラインを通じて実行されます。ファクトリ機器をスマートセンサ、PLC/エッジコンピュータ、およびMESに接続することで、現場の機器は、ユーザ/OEMが開発したプログラムをダウンロードして、自動チェンジオーバコマンドに従ってインテリジェントな手順を実行することができます。この結果、生産プロセスでの中断を最小限に抑えられビジネスを継続できます。
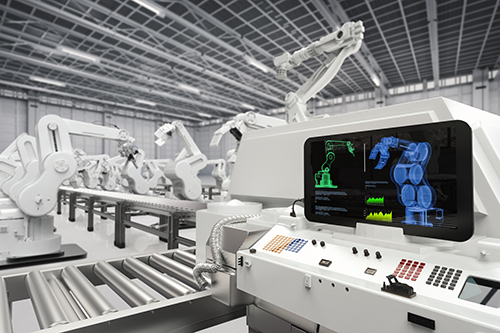
一般的に言って、相互接続されたファクトリのシナリオとしては、製品IDなどのデータを抽出するために、ファクトリ機器に接続されたシリアルデバイスサーバと有線またはワイヤレスの産業用ネットワーキングデバイスが必要になります。次に、ワイヤレスアクセスポイントやイーサネットスイッチなどのネットワークハードウェアを使用して、情報をMES/DNC(Direct Numerical Control)サーバに転送します。MES/DNCは、ネットワークを介して接続されている各ファクトリのマシンに切り替えコマンドとGコードを転送します。このプロセスにより、CNCマシンとロボットはより多くの情報をダウンロードしてアダプティブスマートマシンになり、効率的にタスクを実行することができます。
最適なスマートマシンは、同じベースマシンプラットフォーム上の異なるプロダクションモジュールを使用して状況に応じて臨機応変に自分自身の再構成のチェンジオーバを実行することができます。システムのダウンタイムを削減し、生産効率を高めるためにサイズとフォーマットの変更をコンスタントに適応することができます。この適応型インテリジェンスを有効にすることで生産ラインは、稼働し続け、次のオーダを生産し続けます。しかしながら、混合した生産シナリオでは、MES(Manufacturing Execution System=製造実行システム)は、限られたコンピュータ機能を使い、より多くの調整コマンドを処理する必要があります。この余分な負荷を軽減するために、エッジコンピュータは、MES (プロダクションループの) の部分的な意思決定を処理する上で重要となる役割を果たします。エッジコンピュータは、通信の待ち時間を減らし、MESコネクションがドロップオフされた場合に、ループの生産プロセス全体を自律的に実行することで生産に対するあらゆるリスクを防止します。
予知メンテナンスとリアルタイム監視
自己監視は、マシンがメンテナンスや修理が必要かどうかを検出するために自己テストを実行することを可能にする内蔵 test (BIT)メカニズムです。一般的なテストは、温度、電流、電圧、モータのトルク、または通信品質のためのものであり、例えば、ロボットアームのトルク出力の低下またはCNC モータの過熱/振動などがあります。しかしながら、潜在的な問題を特定した後でも、技術者の接近性が制限され、運用時間中にサイトで問題を確認するためにコストがかかる可能性があります。更に、企業の管理者は、資産の運用パフォーマンスとその可用性を監視できるように、システムのオンラインが必要とます。

マシンデータを収集し、システムをクラウドに接続することにより、ファクトリおよびマシンのリモートリアルタイム監視とリモートメンテナンスが可能になります。マシンのパフォーマンス、システムステータス、そして更に重要なハードデータを完全に透過することにより、管理者は、現在のマシンのパフォーマンスの維持を追跡することができます。オペレータは、許容範囲外のパフォーマンスの変動を予測するために同様のマシンの履歴データを見ることができます。この豊富なデータを使用してソフトウェアエンジニアは、アラームごとの発生に基づいて数学モデルを構築してマシンの故障を予測できるためオペレータが積極的にメンテナンススケジュールを立て、平均修理時間(MTTR)を改善しダウンタイムおよび修理による利益損失を軽減します。また、このリアルタイムの情報とリモート接続されたメンテナンスソフトウェアとを組み合わせることで、コストのかかる問題が発生する前にオペレータがマシンをリモートでメンテナンスサービスを実行することができます。この知識を承知の上で技術者は、ダウンタイムを回避するためにピークの稼働時間外に到着するようにスケジュールを組むことができます。
Moxaのソリューション
Moxaでは、スマート製造を実現するのに役立つ幅広い統合ソリューションを提供しています。スマートマニュファクチャリングソリューションの詳細については、コネクティビティ、ネットワーク、それを結び付けるコンピュータハードウェアの詳細な内容を含んだスマートマニファクチャリングのブループリントをご覧ください。